An interview with Willy C. Shih, professor of management practice, HBS’s technology and operations management unit. Read the complete article, “Can America Compete?” (September-October 2012)
Harvard Magazine: You’ve had a lot of manufacturing experience.
Willy Shih: I spent 28 years in industry. I confronted a lot of puzzles there, and I’ve been looking at them since coming here.
The interesting question relating to competitiveness had to do with my time at Kodak. In 1997, I took over the consumer digital business it was trying to build. That year Kodak shipped a few tens of thousands of digital cameras. One of the factories in Rochester, New York, had this highly automated assembly line where the engineers were attempting to manufacture digital cameras locally. You needed a whole bunch of electronic and optical components: electronic sensors, the tiny displays that show you your pictures, rechargeable batteries, consumer-electronic stuff.
I found that back in the 1960s and 1970s, all the money in photography was made manufacturing film. So Kodak let go of camera manufacturing except for the low-end, single-use cameras—basically just a box for film with a lens. In the same decades, U.S. consumer-electronics makers outsourced the assembly of TV sets to Asia, and then they gradually let go of more and more of the business.
So I arrive in Rochester and find that there is no more expertise in the U.S. for all the components you need to build a digital camera—not in LCD displays, electronic sensors, zoom lenses, or the tiny electric motors you need to drive zooms. There weren’t people who made shutter buttons or view finders, or any of those components. So even though my team had decided we were going to be highly automated, you couldn’t design and make digital cameras in the U.S. That was the first object lesson.
That was repeated when I took over the organic LED (OLED) business. Kodak made the pioneering invention in organic electroluminescence. In solar photovoltaic cells, it’s light in, electricity out; this is electricity in, light out. There are a lot of benefits to this technology; a Samsung Galaxy S smartphone has an OLED display. But the path to market required the ability to make extremely uniform, low-temperature polysilicon on glass. It was the same story: even though U.S. companies invented a lot of the technologies, they had given up on commercializing and manufacturing them, so there was no way for us to get to market in the U.S.
That led to my thinking about the similarity to the tragedy of the commons—the loss of the shared pastures in a town that nurtured all the farmers’ animals. All these predecessor organizations had let these capabilities go because they didn’t matter to them individually at the time—but they turned out to be critical if you wanted to go into some important new technologies. It raised the question: if you don’t have capabilities in some of these areas, does that mean it no longer makes sense to invest in research and development and innovation in other new areas? Gary Pisano [Figgie professor of business administration] and I pointed out in a 2009 Harvard Business Review article that you couldn’t make an Amazon Kindle in the U.S. because many key capabilities no longer existed. The key technology in that device came out of MIT: the electrophoretic beads for its e-paper display. It was commercialized by E Ink here in Cambridge. But they had to go to Asia to make the complete screen.*
HM: What caused this dispersal of manufacturing?
WS: When I grew up in industry in the 1980s, the thing they always pounded into an engineer’s head was the importance of product development and commercialization being close to production. When I was at IBM in Austin, our factory was across the road; when your processes are not particularly mature, it really makes sense to be close to production.
So why did everyone start outsourcing? When the Asian economy—specifically China—opened up, the labor-cost differential was so great and there was such a limitless supply, seemingly everybody focused on labor arbitrage. My fully loaded labor cost in Rochester in the late 1990s was more than 100 times higher than China’s. Everybody just moved their manufacturing over there.
Now what happens if your engineers and designers have to be close to manufacturing? Well, we just fill the sky with planes. If you’re on the product side of Apple, you spend a lot of time in China—near the factories, working out problems.
The core question is whether this affects your ability to innovate. Gary and I think there is an impact, especially in leading-edge technologies where manufacturing processes are not yet mature. So we’ve just called that out.
Part of the problem is that people don’t think of manufacturing as knowledge work. They think of it as someone putting in four screws 2,400 times a day—and there is a lot of that in the more mature assembly areas. But in a lot of manufacturing, a lot of value is created in commercialization and advanced manufacturing; a lot of that is sophisticated knowledge work. If you wander around in factories around the world (since the beginning of 2011 I’ve been in more than a hundred factories), you see some very sophisticated knowledge work. In some of the advanced semiconductor fabrication lines in Asia, you have masters in engineering running production tools that cost as much as an airplane—$65 million, $70 million. They’re extremely sophisticated and complex, and a lot of engineering goes on on the factory floor.
So one of the things we call out is that conception that manufacturing is not knowledge work. For some types of manufacturing, it is very important to maintain production capability because it’s tied to your ability to innovate.
HM: Do you see a similar fate for some of the new industries American businesses have been counting on?
WS: Photovoltaic panels are a problem because America has let go of a lot of the electronic supply chain and silicon-processing skills from semiconductors. The companies that manufactured semiconductors—that commons fed the flat-panel-display industry, the solar-panel industry, the energy-efficient lighting industry with LEDs, because a lot of the same capabilities flowed into those.
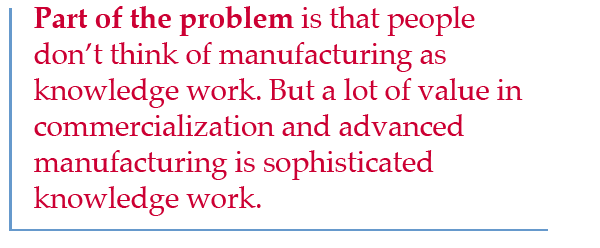
HM: What about areas of U.S. strength like aerospace assembly, biotech, and medical devices—what are the risks there?
WS: The same kinds of things. A couple of factors led to unquestioned U.S. manufacturing leadership at the end of the 1960s and early 1970s. We had institutional foundations and broad education in the practical arts, going back to the Morrill Land Grant Act. We controlled mass manufacturing going back to the nineteenth-century “American system of manufactures,” with interchangeable parts and gages, specialized tools, sequential production—all leading to Henry Ford and mass assembly of automobiles. And at the end of World War II, all our competitors were in ruins. At the end of that war, we had this public perception that science had won the war—not just the atomic bomb, but things like radar, antibiotics, the proximity fuse, and countless other innovations. So as a country we had a lot of faith in science, and we invested heavily in our basic science and education.
But other countries did, too—Germany and Europe, but also Japan, the Asian tigers, and China. Now other countries compete very aggressively for those manufacturing facilities. Singapore would love to be the biotech hub of the world: they are competing very aggressively for R&D and manufacturing facilities. Every other Asian country is asking those questions as well: how do I capture more of these export-earning industries?
We haven’t thought about preserving those types of capabilities. There are some industries where we’re still pretty strong, like aerospace, especially jet engines—the engine manufacturers are pretty thoughtful about what is important to hold on to. But lots of other countries have decided what’s important. In the capital-equipment businesses these days, if you’re going to sell in a lot of countries, you need to provide production offsets for local manufacturers—so they begin picking up the skills and learn how to move to higher value-added.
I worry about composite materials, where the U.S. has really had a lead. We’re shipping a lot of that overseas. I worry about biotech manufacturing and medical devices, where we have a lot of regulatory issues—Europe is a lot easier for medical devices, so we’re chasing a lot of the companies that make them offshore.
It’s a complex mix of factors, but again the key in my mind is preserving innovative capability. We talk about innovation a lot, but we don’t recognize how important making things is to preserving some of that innovative capability over time.
HM: What are the relative responsibilities of businesses and of policymakers in preserving those innovative capabilities?
WS: Managers need to think longer term about those capabilities and about the context in which they’re embedded. It’s not only the people and knowledge within their walls—it’s their supplier network and competitors in adjacent industries. Thinking about capabilities is key.
The government has to correct some of the policy deficits that caused the U.S. to be less favored as a location. Mike and Jan’s survey of HBS alumni showed how few companies would actually choose to locate in the U.S. In some industries, location decisions are heavily influenced by tax incentives. But I can absolutely say that our complex tax law and relatively high rates of taxation motivate people to move operations offshore. So the government needs to think about how we at least get to a level playing field and it has the responsibility to invest in public goods: basic scientific research, education, and infrastructure—key parts of the “commons” that private companies are incapable of investing in.
HM: What skills would the U.S. need to promote to tilt decisions about where to locate operations away from a strictly financial calculation about the cost of hiring suitable employees?
WS: Once you allow those skills to dissipate, throw away those capabilities, a lot of those decisions are very expensive or impossible to reverse. My counsel is to be more thoughtful about that.
I just wrote a case on a large multinational that has its engineering center in India, with thousands of engineers and an average age of 27, and its home engineering operation in the U.S., where the average age is 47. The guys in India said the U.S. operations hadn’t hired anybody in the past half-dozen years, so they don’t have fresh skills. Do you retrain, or start with the younger generation and try to keep their skills fresh? That’s a huge problem. I saw people at Kodak in film manufacturing who had amazing skills, but as technological substitution happens, those people can’t take their skills anywhere.
The global market for tradable goods decimated the lower- skilled jobs. I think it’s starting to attack highly skilled jobs, too. I don’t have good answers, but I think that’s the next huge issue.
Next: Compensation Practices and Incentives
“The first step is popping the myth that we can use financial markets naively to measure performance over short horizons…”
Mihir A. Desai, Mizuho Financial Group professor of finance and professor of law, and HBS’s senior associate dean for planning and university affairs